The Multi Solid Fuel Fired Hybrid Steam Boiler With Fluidised Bed Combustor
The Combipac (CPFD) is a hybrid smoke and water tube design boiler, with the combustor
based on the principle of Fluidised Bed Combustion (FBC). The fuel bed is fluidised by the
injection of air from the bottom of the bed, through a set of air nozzles, using an FD fan. This
produces a fuel bed resembling a boiling fluid, which helps achieve uniform mixing and
efficient combustion.
In this Combipac – FBC range of boilers, the higher turbulence levels, better residence time,
low excess air and uniform distribution of air and fuel improve overall combustion efficiency.
These Combipac boilers also offer the flexibility of firing a wide variety of low cost agro-waste
and other low grade solid fuels efficiently.
Product offering
- Capacity: 4,000 to 25,000 kg/hr
- Standard Design Pressure: 10.54 & 17.5 kg/cm²g (models available up to 32 kg/cm²g)
- Fuel: Paddy Husk, Coal, Lignite, Groundnut Shell, Petcoke, Sawdust, Wood Chips and Biomass pellets

Membrane Panel Assembly
The furnace enclosure, in the Combipac, has a unique ‘D’ type membrane panel design with integrated in-bed tubes, for optimized heat transfer in the radiation zone.
Salient Features ‘D’ Type Membrane Panel
- The CPFD series has a special ‘D’ type membrane panel assembly, which connects the in-bed header assembly with membrane panel assembly, to achieve higher circulation and circulating water velocity.
- Eliminates the need for a bigger pipe to connect the membrane panel assembly to the shell, thereby reducing the number of gussets as well as stress concentration on the shell tube plate.
- Distance between the membrane panel assembly and bed is optimised for effective radiative heat transfer. In conventional ‘V’ type membrane panels, the higher distance between membrane panel assembly and bed reduces the view factor and subsequent heat transfer.
Tube-Strip-Tube construction
- In the Combipac CPFD, membrane panel assembly tubes are joined with strips to provide additional heat transfer area and eliminate flow restriction. Also, reduction in the number of tubes yields higher circulation velocity and avoids phase stratification.
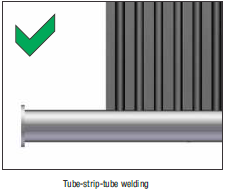
- In Tube-tube construction, the circulating velocity is reduced, due to the larger number of tubes, which can lead to overheating. Hence this type of construction is not recommended.

Shell Assembly
Salient Features
- Efficient convective pass design
The Combipac CPFD shell is of single pass design, with tubes of optimally sized diameters eliminating the turning of flue gas in the convective bank and, thus, reducing tube and tube plate erosion.
- Better steam quality and load response
Higher steam/ water interface area and higher freeboard together ensure better steam quality. The Combipac CPFD shell is also designed for large water holding capacity, thus ensuring better response to fluctuating loads.
- Wire coil inserts
The convective bank tubes are provided with wire coil inserts to improve flue gas turbulence and velocity near the tube wall, thereby improving heat transfer performance.
- Simple layout
The position of the smoke chamber with hinged doors reduces complexity in the layout and facilitates easy cleaning.
Fluidised Bed Combustor (FBC)
The combustion zone in the Combipac CPFD comprises a plenum chamber with a set of air nozzles, air distribution system and settling chamber.
- Cycloidal air injection
The boiler comes with the unique Cycloidal Air Injection Technology that improves combustion efficiency. The cycloidal motion of the secondary air aids in achieving higher residence time of fuel in the combustion chamber. This technology also improves turbulence in the furnace, and reduces the amount of excess air required for combustion of fuel.
- Air distribution nozzles
The air nozzles and furnace region have been designed to optimise Time (residence time), Temperature (furnace temperature) and Turbulence, thereby facilitating high levels of combustion efficiency.
- Settling chamber
This helps collect heavier particles and unburnt fuel in the furnace region, thus safeguarding the convective bank from choking, and also preventing flame impingement on the tube plate due to fuel carryover.
Combustion chamber assembly

In-bed tubes
The membrane panel in the Combipac CPFD is provided with integrated in-bed tubes to recover heat from the radiation zone and maintain uniform bed temperature.
Salient features
- In the CPFD’s in-bed header design, all bends have been placed outside the fuel bed zone. This helps eliminate erosion problems.
- The in-bed header tube in the CPFD, with its higher pitch, helps to achieve lower air and particle velocity between in-bed header tubes. This also helps to reduce erosion problems.
- The CPFD in-bed header has been designed with very high circulation ratio and water velocity, to eliminate tube overheating problems.
Fuel feeding system
Combipac CPFD comes with various fuel feeding options, which offer the flexibility to fire a wide variety of solid fuels in this boiler.
- Under Bed Feeding (UBF)
The under bed feeding system is suitable for fuels like rice husk, Indian coal, Indonesian coal, lignite etc. The under bed feeding system consists of a rotary feeder and a booster fan.
- Over Bed Feeding (OBF)
The over bed feeding system in the boiler is suitable for fuels like Indian coal and paddy husk. The over bed feeding system features a screw feeder.
Safety and Instrumentation
- Combipac CPFD comes with instrumentation of and a high level of high standards and a high level of safety interlocks that, together, ensure safe and reliable operation of the boiler. Safety interlocks provided with the standard unit monitor flue gas temperature, outlet steam pressure and water level in the shell.
Optional accessories
A range of optional accessories can be provided with the Combipac CPFD to further enhance efficiency, control outlet emission levels, automate operations and increase safety interlocks.
- Pollution control equipment
Pollution control equipment such as Multiclone Dust Collector (MDC), Cyclomax, Bag Filter and Electrostatic Precipitator (ESP) can be provided to control particulate emission levels.
- Automation
High levels of automation to control water level, steam flow and water flow can be offered as add ons. Also, Programmable Logic Control (PLC) with Supervisory Control and Data Acquisition (SCADA) system can be offered.
Technical specifications

General arrangement
